This is a Herbert Schmidt SA that I've been doing some work on and thought I'd share the process I use to make grips.
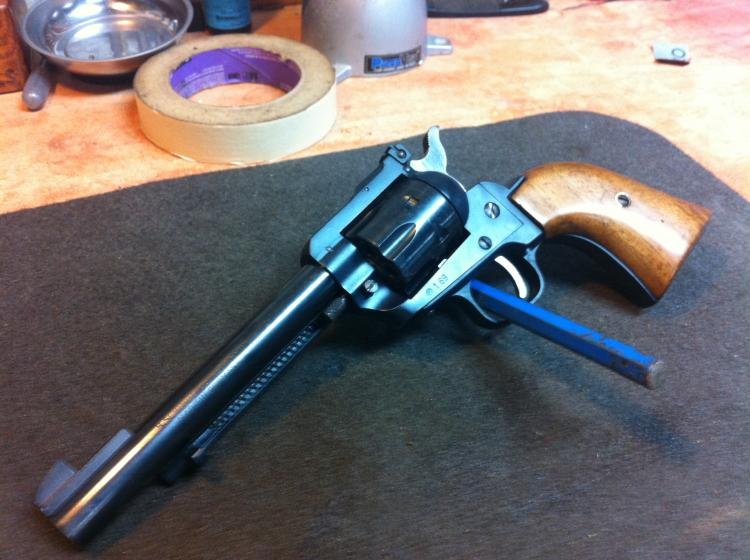
The existing grips don't seem to fit after someone did a little to much sanding.
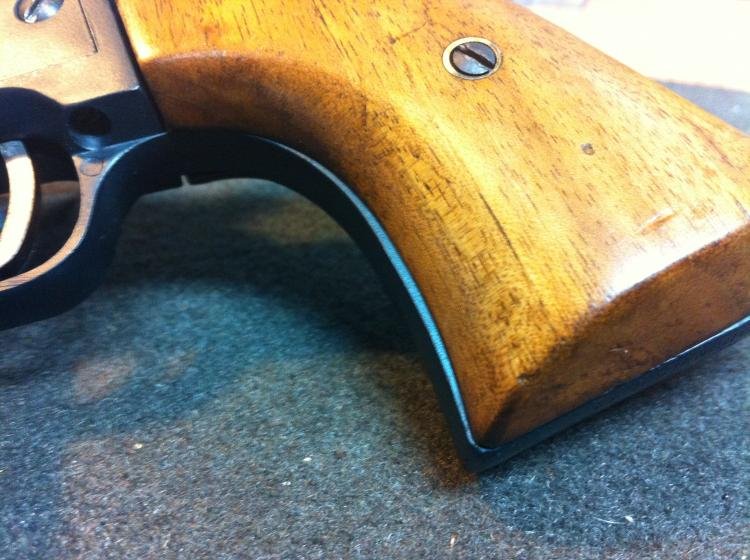
Step 1: Template
I like to use clear overhead projector sheets for my templates. (I'll exlpain why as I go). Trace with a sharpie so you get a wide line around the grip and trim to outside edge of line.
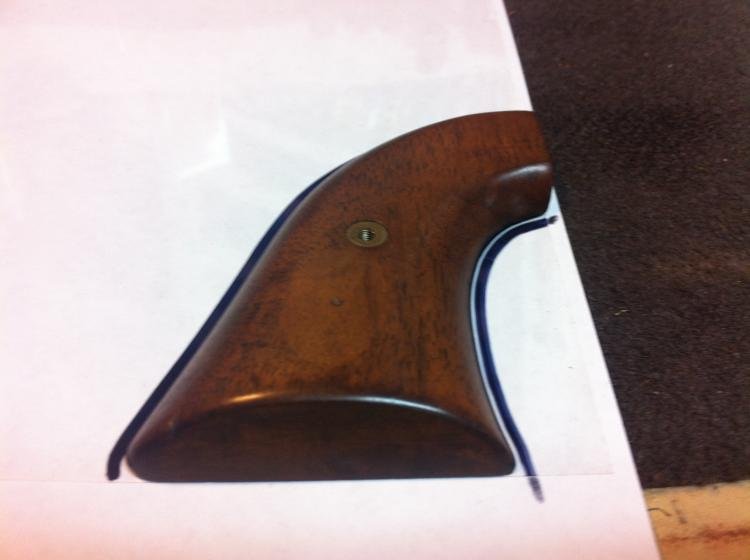
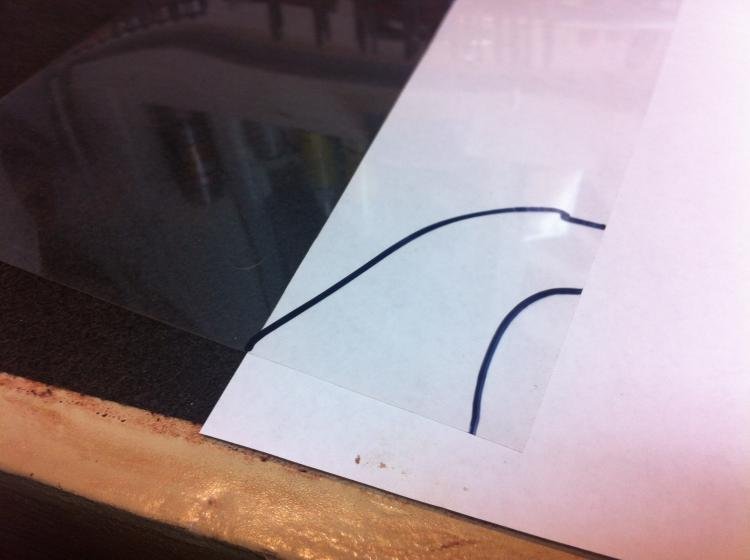
Let's go ahead and protect that new Socom Blue Cerakote finish with some painters tape and then trim off overhanging tape with a razor.
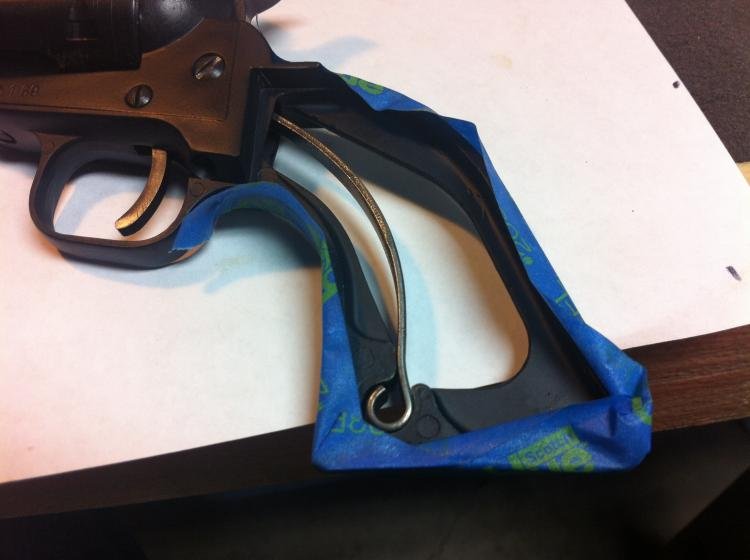
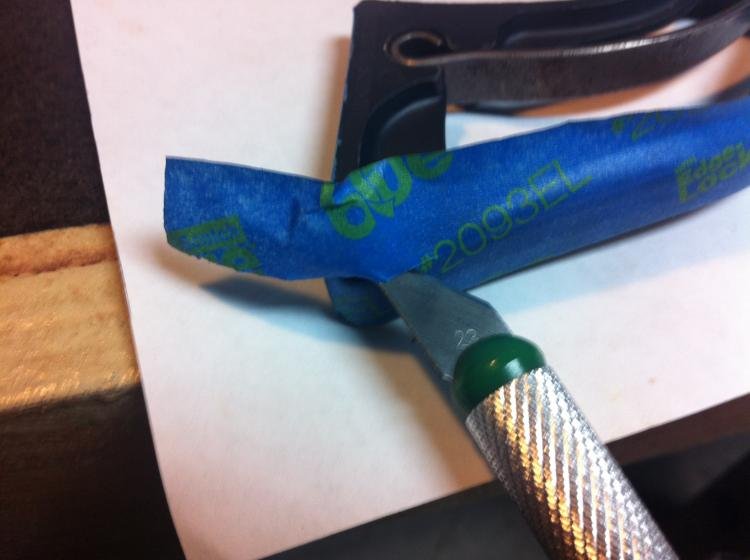
Now trim the notch next to the reciever for a perfect fit and then hold the existing grip up tight to the frame and punch the hole for the grip screw.
This is reason #1 for using transparency.
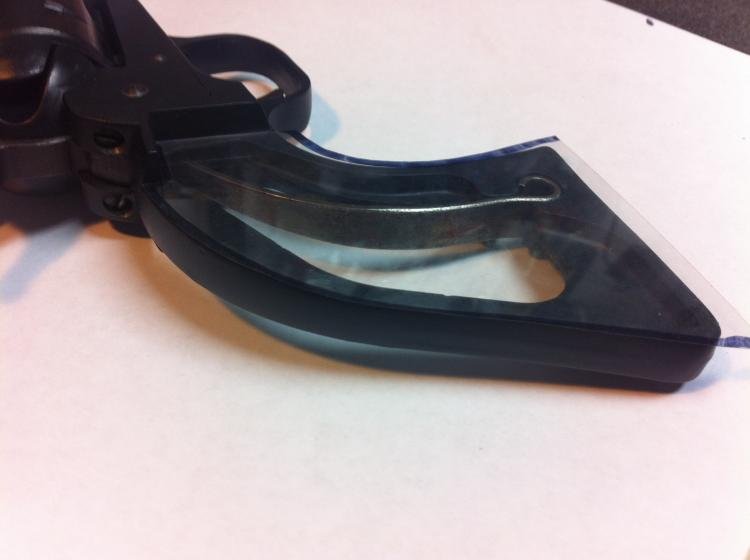
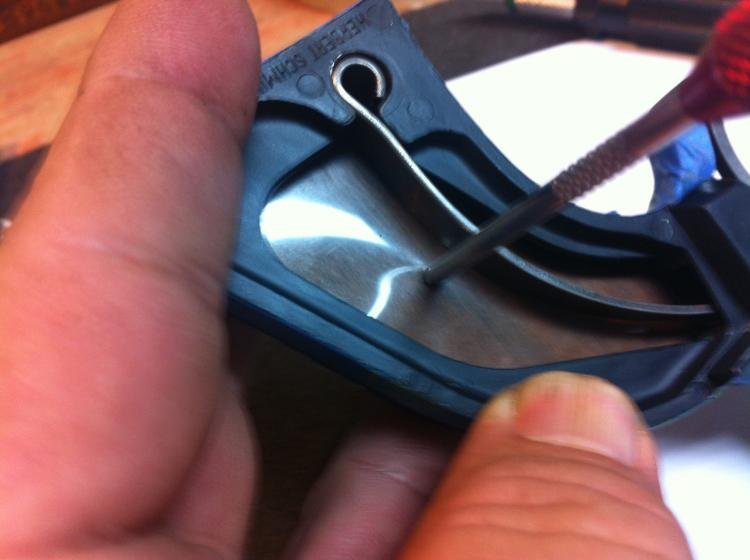
Put the grip pin in and then screw down both grips so the grip pin puches the locating hole for the pin.
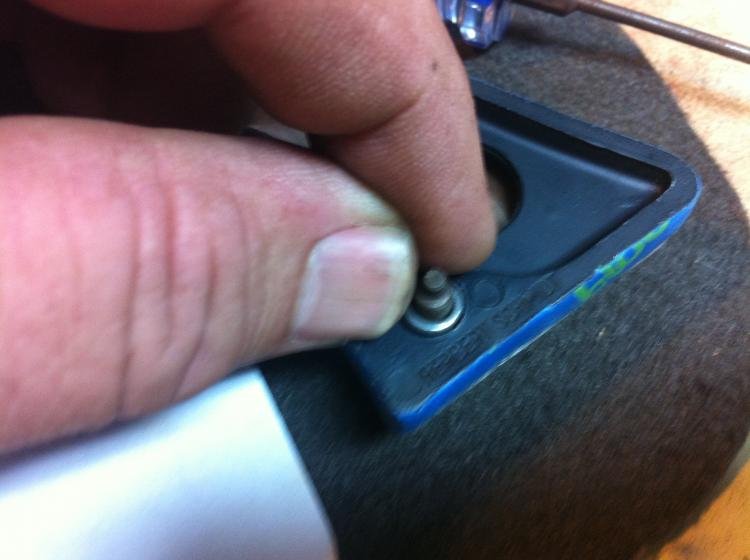
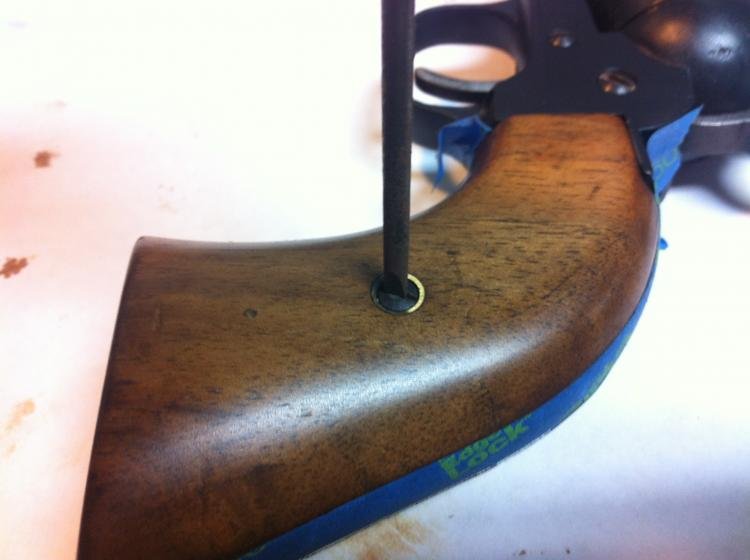
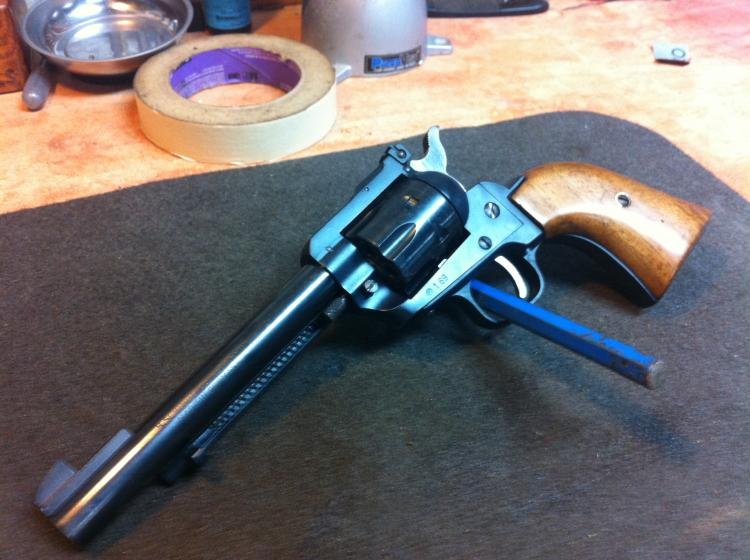
The existing grips don't seem to fit after someone did a little to much sanding.
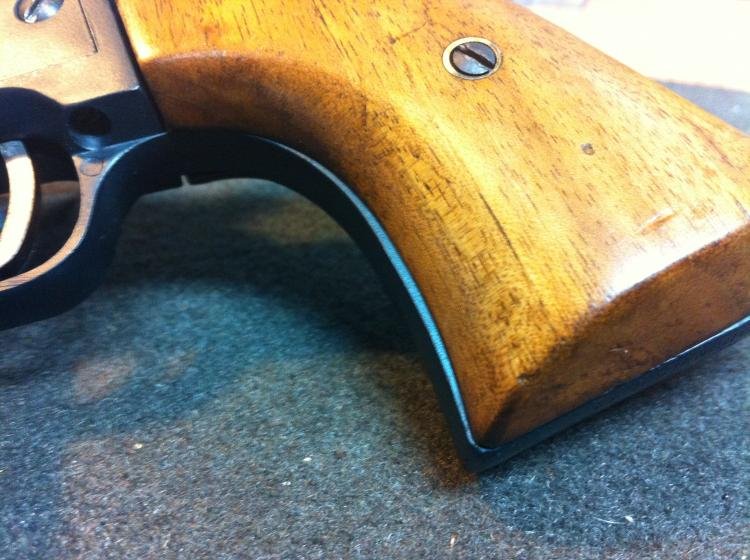
Step 1: Template
I like to use clear overhead projector sheets for my templates. (I'll exlpain why as I go). Trace with a sharpie so you get a wide line around the grip and trim to outside edge of line.
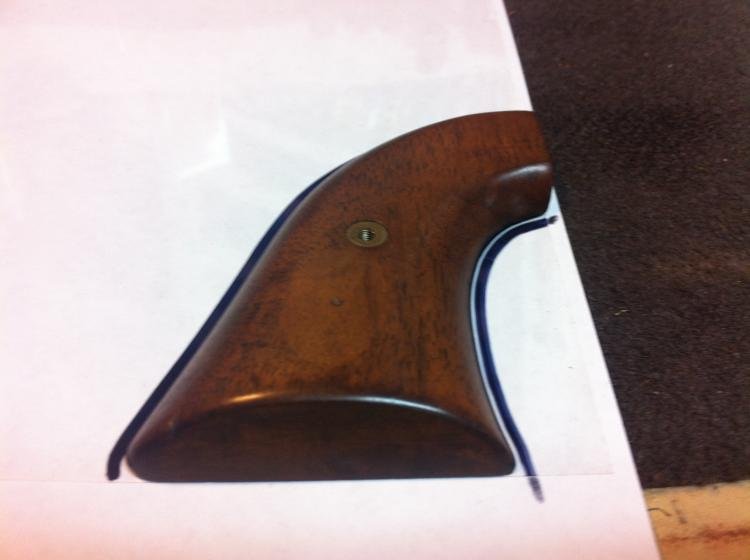
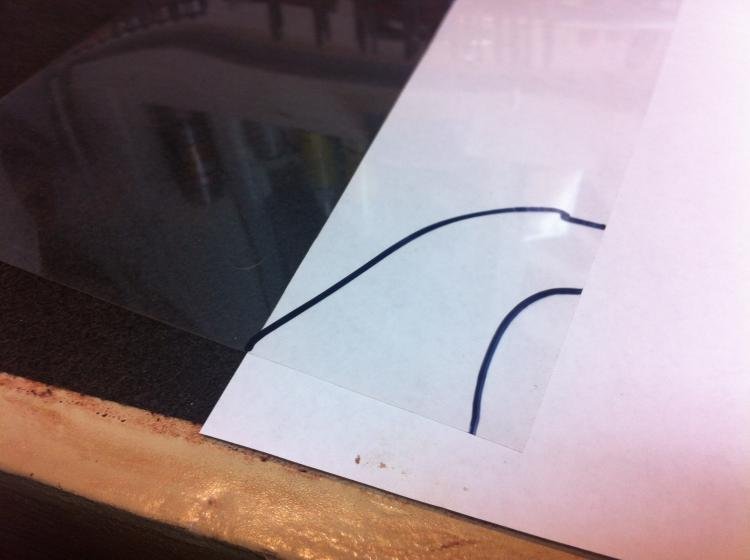
Let's go ahead and protect that new Socom Blue Cerakote finish with some painters tape and then trim off overhanging tape with a razor.
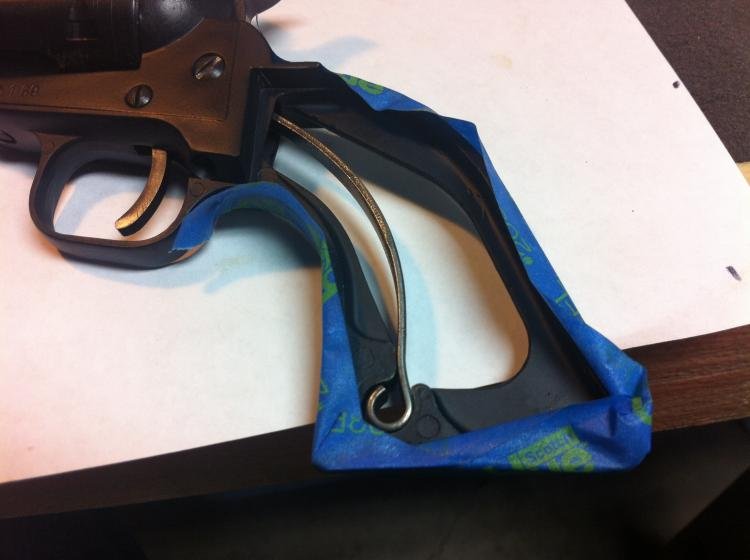
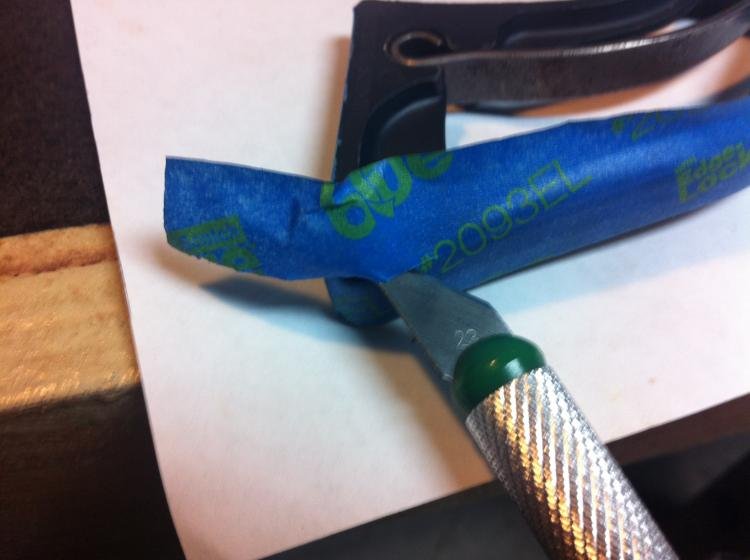
Now trim the notch next to the reciever for a perfect fit and then hold the existing grip up tight to the frame and punch the hole for the grip screw.
This is reason #1 for using transparency.
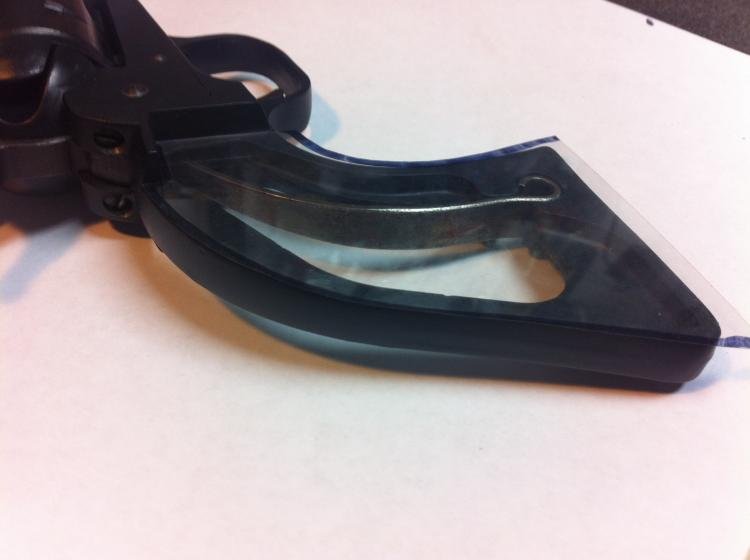
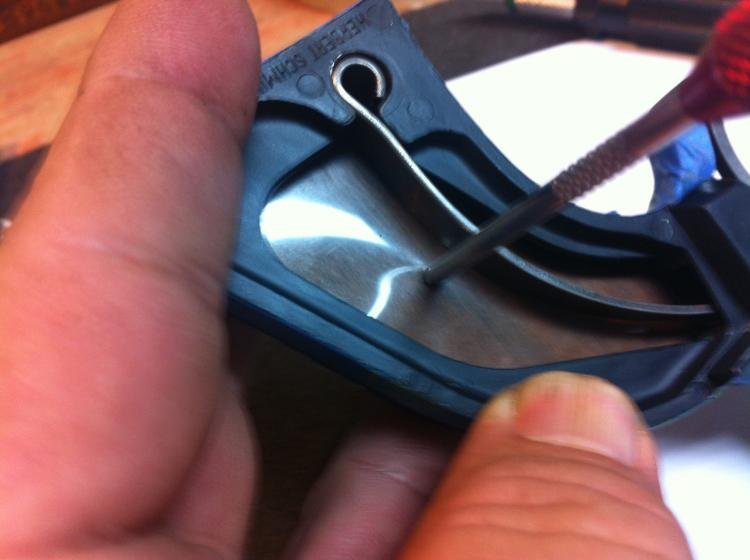
Put the grip pin in and then screw down both grips so the grip pin puches the locating hole for the pin.
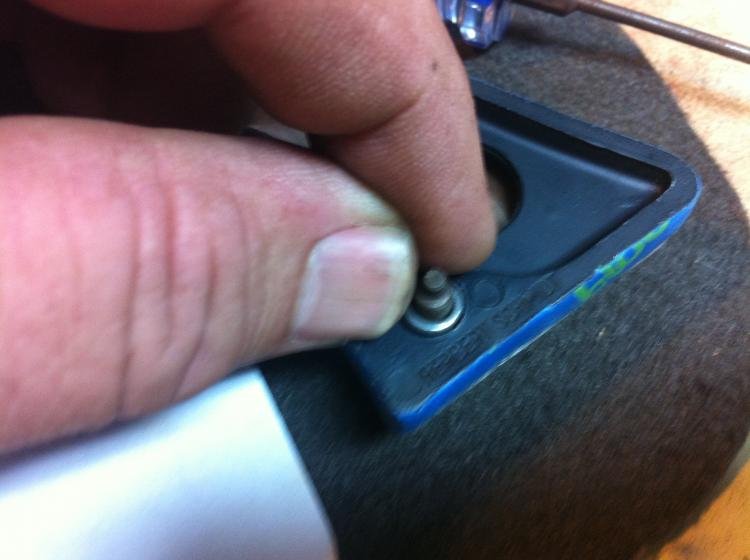
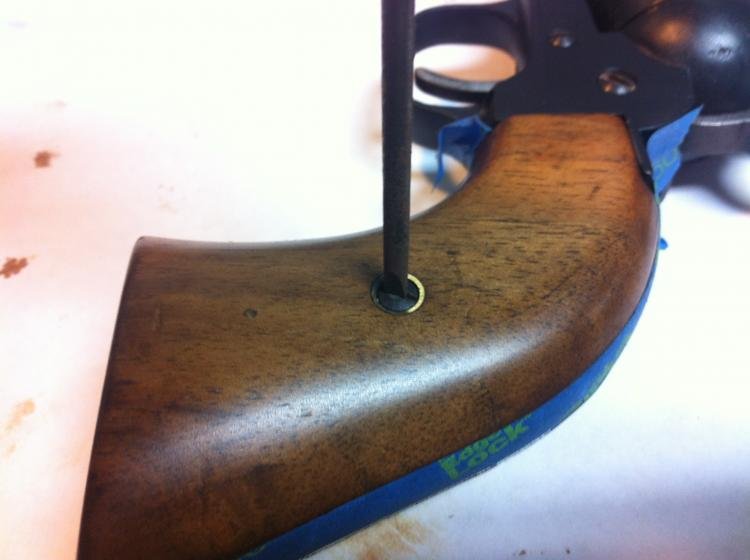
Last edited: